Geocomposites’ Impact: Advancing Metal Forming with Four-Slide Stamping
Metal stamping is an economical manufacturing method that uses pressure, a die surface, and tooling to produce precision metal components in large quantities. This high-speed metalworking process encompasses a variety of cold-forming techniques like bending, cutting, blanking, punching, and coining that shape a workpiece from sheet metal.
Some metal stamping techniques are more cost-effective than others, however, with two of the more affordable options being progressive die stamping and four-slide stamping. Both of these methods offer advantages that make them suitable for creating diverse components.
Four-Slide Stamping and Its Versatility Another metal stamping technique that’s gaining attention due to its versatility in shaping diverse materials, including geosynthetic materials and geogrid, is four-slide stamping, or multi-slide stamping. This process forms the metal into designated shapes using four tools that move laterally, all at the same time. The four slides efficiently stamp, cut, bend, or otherwise form a metal sheet, striking it orthogonally as the material feeds through the machine. Four-slide equipment is capable of producing multiple folds or punches in a single step.
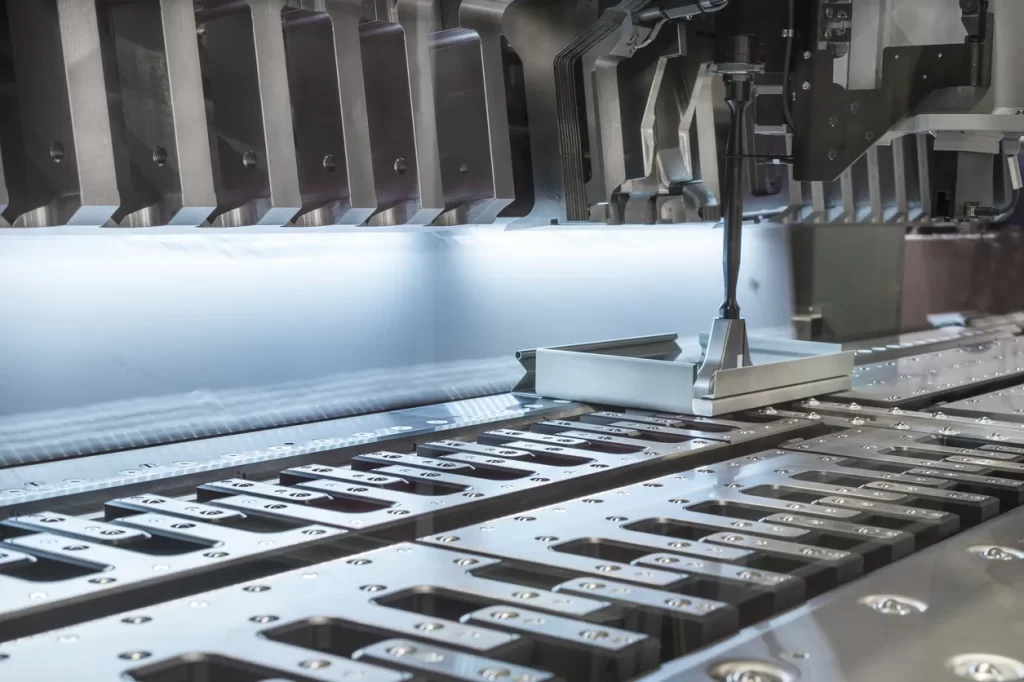
This stamping technique is beneficial for its:
- Comprehensive operations: Machinery performing four-slide stamping will use one single operation to complete several stamping and forming processes. As a result, manufacturers benefit from a start-to-finish procedure that doesn’t require any secondary operations to complete a component.
- Design and material versatility: Four-slide stamping forms metal from multiple directions, giving you greater flexibility to generate complex designs with intricate, unique configurations. Additionally, four-slide stamping is compatible with a wide variety of materials, such as aluminum, copper, brass, bronze, steel, geosynthetic materials, and geogrid.
- Adaptability: It’s often challenging and time-consuming — not to mention costly — to optimize metal part designs using conventional press systems. In some cases, you need to use a brand-new custom die. However, because of its ability to complete multiple operations, you can simplify metal stamping with a versatile four-slide. It only requires minor modifications to meet the needs of a new component, and this optimal flexibility will save you time, money, and energy.
- Faster turn times: Four-slide stamping offers quick turnarounds through rapid production. Its equipment typically works in conjunction with other processes, which also improves production speeds. Greater throughput and reduced turn times will, in turn, lead to cost benefits.
- Cost-effectiveness: Four-slide stamping is a cost-effective metalworking option because of its efficiency, material use, and minimal waste production. Its equipment can produce small or complex components in high volumes at high speeds while maintaining consistent part quality. In fact, it’s possible to generate around 15,000 individual parts per hour for components featuring simpler designs. All of this is helpful to your bottom line.
Geogrid: Progressive die stamping and four-slide stamping offer cost-effective metalworking solutions. For reliable, IATF-certified stamping services tailored to your project, consider Engineering Specialties, Inc. (ESI). Their advanced automation equipment, quality services, and tight tolerances ensure superior custom results at competitive prices.